From Problem to Profit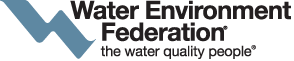
A Fort Worth water resource recovery facility turns industrial waste challenges into energy opportunities
By Kristina Twigg and Peter V. Cavagnaro. Kristina Twigg is the Associate Editor, World Water: Stormwater Management at the Water Environment Federation (Alexandria, Virginia.). Peter V. Cavagnaro is a project development consultant at Johnson Controls Inc. (Milwaukee, Wisconsin).
The Village Creek Water Reclamation Facility in Fort Worth, Texas, lies on Trinity River’s west fork. Every day, the facility treats more than 378,541 m3 (100 million gal) of wastewater. With about 6437 km (4,000 miles) of sewers, the wastewater, carried largely by gravity, can take 8 to 12 hours to travel to the facility. Within this time, flows can become septic, and high-strength industrial wastes can be problematic for local industries to dispose of.
However, the Village Creek plant has turned the problem into an energy solution: Now the facility generates 75% of its electricity onsite.
“The plant’s co-digestion program has shifted the industrial wastes to a point in the plant where their energy can be harnessed,” said Madelene Rafalko, a senior professional engineer at the Fort Worth Water Department. “By injecting these concentrated wastes directly into the digester, the plant has decreased the amount of energy needed for aeration treatment.”
Wastes boost methane production
With the addition of co-digestion waste, the facility has doubled its gas production. However, facility staff are very selective about the wastes they bring in. “We are looking for wastes with high COD [chemical oxygen demand], which are more easily converted to methane,” said Jerry Pressley, water systems superintendent. The plant looks for wastes that produce a high gas yield with low residuals but avoid wastes with sulfides and sanitizers because they can cause process upsets, such as digester foaming, he said.
For 10 minutes every hour, the high-strength wastes are injected into six of the plant’s 14 anaerobic digesters. The plant has been capturing digester biogas for decades and uses it to power one of two 5.2-MW turbines. These turbines generate about half of the plant’s energy, most of which is used for the plant’s aeration system.

Photo 1. The co-digestion building is where the plant receives industrial wastes. Operators ensure that the wastes do not contain chemicals that would upset the anaerobic digestion process. (Credit: Kristina Twigg)
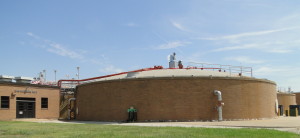
Photo 2. Biogas, used to generate energy via the plant’s turbines, is created in these anaerobic digesters fitted with linear motion mixers. (Credit: Kristina Twigg)
Steam heat provides return on investment
However, the Village Creak Water Reclamation Facility has also found a way to reduce the energy needed for its aeration basins.
In the process of using the turbines to generate electricity, heat is also created. The plant has harnessed this heat to make steam, which powers two of the plant’s blowers. The heat is also used to warm buildings and anaerobic digesters during winter. Even the steam itself is not wasted — it is condensed and reused.
“The cost savings from the steam process has paid for everything else,” Rafalko said. The project, started in 2007, has saved $3 million so far, he said.

Photo 3. The Village Creek Water Reclamation Facility generates both energy and steam. The steam is used to power two of the plant’s aeration basin blowers. (Credit: Kristina Twigg)
Improvements lead to other efficiencies
While the steam process is the largest part of the plant’s energy-efficiency program, staff have also taken advantage of low-hanging fruit, such as optimizing process controls, upgrading pumps and motors, replacing its SCADA system, and installing a web-controlled lighting system. “Going through and taking measures helped us to identify maintenance needs and further energy improvements,” Pressley said.
The plant also created anoxic zones in six of its 13 aeration basins. In the presence of oxygen, bacteria convert ammonia to nitrate (NO3). Then in the anoxic zones, the bacteria can utilize the oxygen present in the NO3. This eliminates mechanical aeration in these sections of the basins, further reducing the plant’s energy needs. These improvements bring the facility one step closer its goal of net-zero energy.
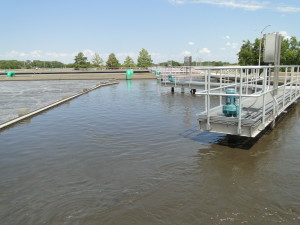
Photo 4. Using anoxic zones in the aeration basin improves energy efficiency at the Village Creek Water Reclamation Facility. (Credit: Kristina Twigg)
Note: The information provided in this article is designed to be educational. It is not intended to provide any type of professional advice including without limitation legal, accounting, or engineering. Your use of the information provided here is voluntary and should be based on your own evaluation and analysis of its accuracy, appropriateness for your use, and any potential risks of using the information. The Water Environment Federation (WEF), author and the publisher of this article assume no liability of any kind with respect to the accuracy or completeness of the contents and specifically disclaim any implied warranties of merchantability or fitness of use for a particular purpose. Any references included are provided for informational purposes only and do not constitute endorsement of any sources.
No comments yet.